Algodão
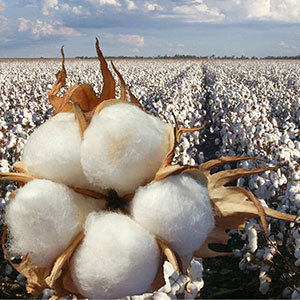
O Algodão
É uma planta da família das Malváceas, do gênero Gossypium. Suas fibras crescem em quantidade considerável, aderidas às sementes e encerradas numa cápsula, capulho, popularmente conhecida como maçã, que se abre quando madura. O algodão é uma planta exigente em matéria de solos, exigindo a renovação dos mesmos mediante o uso de fertilizantes, rotação de culturas, ou ainda, simplesmente, permitindo o descanso dos solos por um certo período.
O algodão é uma planta de clima quente, cujo período vegetativo é longo, aproximadamente 5 meses, e por isso, necessita de verões longos, quentes e bastante úmidos. Na maturação, quando se abrem as cápsulas, a chuva pode se tornar prejudicial. Um clima quente, com duas estações (chuvosa e seca) apresenta condições naturais propícias ao cultivo.
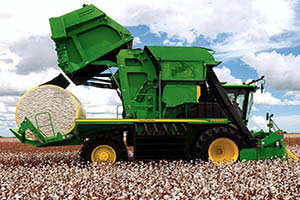
A Colheita
A colheita de produção é feita com colheitadeiras mecânicas, após aplicação de desfolhantes, ou de forma manual,. No Brasil, já é não é mais comum a presença de colheita manual, o que ainda pode ser encontrado com mais freqüência em algumas lavouras africanas e asiáticas. Além de uma regulagem ideal das máquinas, outros fatores que devem ser observados para a manutenção da qualidade da fibra durante a colheita são a limpeza da plataforma, dos fusos e gaiolas das colheitadeiras que recebem o algodão em caroço. Além disso, deve-se evitar a colheita noturna ou em horários em que a umidade esteja alta, evitando assim o “encarneiramento” da fibra no processo de beneficiamento.
Após colhido, o algodão a granel é compactado, formando-se os fardões, que antes do beneficiamento podem ser armazenados por um curto período de tempo. Eles devem ser depositados sobre uma camada de 5 centímetros de “casquinha” seca de cupulho, evitando que o fundo do fardo se contamine com a terra. Em seguida são manuseados e transportados das fazendas até as usinas de beneficiamento.
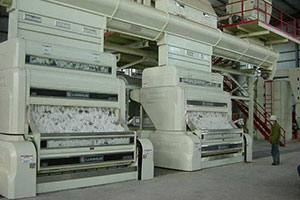
O Beneficiamento
Durante o beneficiamento, o algodão passa por um processo de limpeza, em que no final, são feitos fardos compactados, que no Brasil pesam em média 200 Kg. Seu objetivo é separar a semente (caroço) da fibra, com a mínima depreciação da fibra e obtenção de um bom tipo de algodão. Existem vários modelos de máquinas de beneficiamento, com diferentes números de serras e vários fabricantes. Atualmente, no Brasil, o beneficiamento ocorre em usinas convencionais, que muitos consideram capaz de produzir uma fibra com maior cumprimento e uniformidade mais alta, embora o algodão fique um pouco mais folhado. Já as usinas de alta rotação são capazes de produzir um algodão menos folhado e mais limpo.
O caroço de algodão é tido como subproduto, uma vez que a pluma possui um maior interesse econômico. O caroço do algodão constitui um subproduto muito apreciado por seu azeite comestível e pelo farelo que resulta da moagem de seu resíduo, que então produz a torta de algodão usado na alimentação de gado e fertilizante.
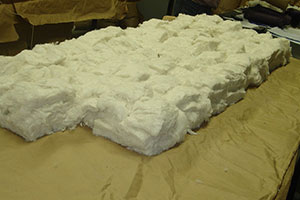
A Classificação
Para cada lote ou fardo de algodão é retirada uma pequena amostra (cerca de 100 gramas) que é então classificada para indicar o tipo do algodão. Existe a classificação visual, em que os classificadores são capazes de avaliar o tipo do algodão, chamado take up. E existe ainda a classificação laboratorial, as amostras são padronizadas e classificadas no qual é realizado através de um aparelho de HVI (High Volume Instrument), que é capaz de classificar entre outros padrões o micronaire, uniformidade, fibra, resistência e maturidade.
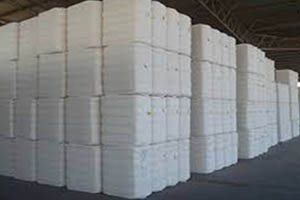
O Armazenamento
Após o beneficiamento, o algodão é armazenado até sua comercialização. Ele pode ser armazenado por longos períodos sem que haja deterioramento de sua matéria, mas com o passar de um ano, sua coloração pode sofrer alterações. Esse armazenamento pode ser feito em armazéns e galpões, ou até mesmo ao ar livre, sendo que neste caso é indispensável que haja uma proteção, como uma lona sem furos, amarradas com barbante, capaz de impedir a penetração de água das chuvas.
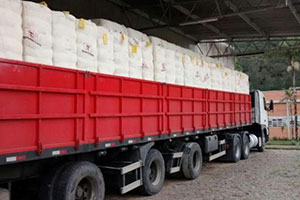
A Logística
A entrega do algodão, no Brasil, é feita basicamente por rodovias em carretas com capacidade para 27 toneladas ou carretas bi-trem, que comportam uma carga de aproximadamente 30 toneladas. Esse transporte é utilizado para a entrega até as indústrias têxteis, ou até os portos, onde são embarcados em navios para o mercado externo. Em todo o processo de transporte, da lavoura para o beneficiamento, da algodoeira para a indústria, e ainda na armazenagem dos fardões no campo ou dos fardinhos no armazém, é necessário a verificação da limpeza dos caminhões, maquinários e toda superfície de armazenagem.
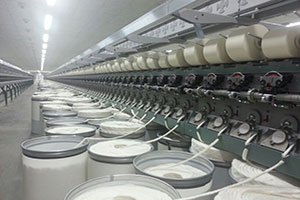
A Indústria Têxtil
Atualmente a fibra do algodão é a mais importante matéria prima utilizada nas indústrias de fios e tecidos. A preferência se deve ao fato de ser mais barata, não requer preparação mecânica nem tratamento químico custoso, ser lavável e mais resistente que a lã. Outra característica interessante é que o algodão é antialérgico, ou seja, não causa irritação à pele ou qualquer tipo de alergia. Além disso ele pode ser facilmente misturado a outras fibras sintéticas, como poliéster e lycra.
A história do algodão começa quinze séculos A.C., quando já se cultivava o algodão na Índia e se fabricavam tecidos com suas fibras. Mil anos mais tarde, os chineses já teciam panos de algodão. Nessa época, ele não era conhecido pelos europeus, que usavam a lã como fibra têxtil comum. A introdução da pluma na Europa é devida a Alexandre da Macedônia (século IV A.C.) e seu uso durante longo tempo foi extremamente restrito. Quando os espanhóis e portugueses colonizaram a América, encontraram o algodão sendo usado pelos nativos do novo continente. Nos E.U.A, a zona algodoeira (Cotton belt) estendia-se pelos estados do sul, desde a fachada atlântica até o Texas.
Há indícios que quando os portugueses chegaram ao Brasil, os indígenas já desenvolviam a cultura do algodão. Ele era cultivado, fiado e tecido. Com o algodão, os índios fabricavam redes e algumas peças de instrumento. Empregavam-no em tochas incendiarias presas as setas.
A Inglaterra em meados do século XVIII, se sobressaiu no desenvolvimento da indústria têxtil, aumentado assim o seu consumo de algodão. Dessa forma, a produção no Brasil, principalmente no nordeste, foi incrementada, visando a exportação. Nessa época ocorreu os inventos dos ingleses Arkwright e Carteright (a máquina de fiar e o tear mecânico), assim como o descaroçador mecânico, desenvolvido por Whitney, que deram extraordinário impulso à utilização do algodão no decorrer do século XIX. Em 1801, a indústria de vestimentas consumia na Europa 78% de lã, 18% de linho e 4% de algodão. Um século mais tarde, as proporções eram de 20% de lã, 6% de linho e 74% de algodão.
A produção norte americana teve declínio no final do século XVIII em função das guerras pela independência, o que também contribuiu para o crescimento da área plantada no Brasil. Já em 1821 a produção dos Estados Unidos cresceu vertiginosamente, em função de novas técnicas e tecnologias adotadas, incrementando suas exportações. Nessa época, no Brasil, muitas lavouras foram reconvertidas para a cana de açúcar, tendo a região do Maranhão, ainda como principal produtor do algodão, seguidos do Ceará, Pernambuco e Bahia.
Outro momento importante foi durante a Guerra de Secessão nos EUA, entre 1861 e 1865, em que o fornecimento para a Europa foi consideravelmente reduzido. O preço foi para as alturas, o que motivou produtores do Brasil, Turquia e Egito e demais países a retomarem a cultura da fibra branca. Em pouco tempo o algodão se tornava o segundo produto mais exportado do Brasil, ficando atrás somente do café. Porém, por volta do ano de 1880, o fim da Guerra Brasil X Paraguai e a desvalorização internacional da pluma, fizeram com que a febre do setor algodoeiro no Brasil fosse rompida.
Após a redução do plantio, a produção nacional se destinou basicamente ao abastecimento do parque têxtil brasileiro, que surgia no final do século XIX. Com a I Guerra Mundial, as exportações da pluma brasileira foram aquecidas. Já em 1917 surgiu a primeira bolsa de commodities agrícolas do país, a Bolsa de Mercadorias de São Paulo. No ano seguinte, o algodão começou a ser comercializado por essa mesma bolsa.
A década de 30 representou um marco para a cotonicultura brasileira, já que após a crise de 1929 o cenário econômico mundial foi abalado. O algodão pegou carona nesse panorama e diante do desenvolvimento das indústrias têxteis e do colapso do setor cafeeiro, se firmou como uma das principais atividades econômicas do país, tendo o estado de São Paulo como maior produtor. Para se ter uma idéia, a área cultivada passou de 343 mil hectares em 1935 para 1 milhão de hectares em 1936. Este crescimento foi contínuo até 1945, quando teve início uma redução da produção. Ela só foi retomada a partir de 1952 com um alcance na produção de 500 mil toneladas de pluma. Na década de 60 o algodão alcançou um posto significativo na exportação brasileira, sendo o segundo maior produto na obtenção de divisas.
As décadas de 70 e 80 foram marcadas pela intervenção do governo no mercado de algodão, o que contribui para que o algodão brasileiro perdesse espaço no cenário internacional. Apesar do aumento de produtividade nesse período, a área plantada foi reduzida de mais de 4 milhões de hectares no decorrer da década de 70, para algo em torno de 2 milhões de hectares no final da década de 80, segundo a Conab.
A década de 90 também foi bastante crítica para a cotonicultura brasileira. Como se já não bastasse problema de pragas e a queda da produção, o governo abriu o mercado para o algodão externo, expondo o produto brasileiro à concorrência dos produtos importados, subsidiados em suas origens. A formação do Mercosul, também facilitou para que algodão proveniente da Argentina e Paraguai entrasse mais barato no Brasil. Uma grave crise foi instalada no setor do algodão e na indústria têxtil. A produção nacional de pluma reduziu-se de 665 mil toneladas em 1989/90 para 410 mil toneladas em 1992/93. Nesse mesmo período as importações passaram de 86 mil toneladas para 400 mil toneladas.
A partir de 1994 com o Plano Real, a economia passa a respirar, e a produção de algodão tem uma ligeira alta. Porém, as importações logo são retomadas, e as exportações reduzidas, em função da valorização do real frente ao dólar. Após safras fracas em meados da década de 90, a partir de 1999 o panorama sofre mudanças. Com a desvalorização do real, as importações são reduzidas e as exportações e tornam cada vez mais atrativas. A produção tem um crescimento significativo, com a consolidação do centro-oeste como principal região produtora nacional.
Hoje, a cotonicultura brasileira tem um perfil bem diferente daquele que apresentava décadas atrás. As novas regiões produtoras (leia-se centro Oeste do Brasil e Oeste da Bahia) possuem alta tecnologia na lavoura, na colheita e no beneficiamento do algodão, além de uma alta produtividade. A média de área plantada por agricultor, que no século passado era de aproximadamente 50 hectares, hoje chega a ser de 700 hectares na região centro-oeste. As importações já não são tão freqüentes e grande parte do volume produzido é destinado às exportações, sendo que a outra parte da produção abastece o mercado interno, o que torna o Brasil um país auto-suficiente no algodão.
Beneficiamento do algodão
Existem no Brasil, atualmente, cerca de 232 usinas responsáveis pelo primeiro beneficiamento (descaroçamento) do algodão, denominadas algodoeiras, localizadas em vários Estados produtores da commodity.
Realizado nas algodoeiras, previamente à industrialização do algodão, o método de beneficiamento consiste na separação da fibra e das sementes por processos mecânicos, com mínima depreciação das qualidades intrínsecas da fibra, de forma a comercializar um bom tipo de pluma de algodão que atenda às exigências das indústrias de fiação, tecelagem e têxtil.
Etapas do Beneficiamento
Pesagem, avaliação de umidades e variedades
A pesagem é a primeira etapa na recepção do fardão de algodão em caroço na usina, momento em que é retirada amostra para avaliação de transgenia, seguida de levantamento do grau de impureza da matéria-prima e do seu percentual de umidade – quanto mais seco o algodão a ser beneficiado, maior a preservação das qualidades intrínsecas da fibra –, fazendo-se então o registro do fardão e o seu encaminhamento para imediato processamento ou armazenamento em pátio apropriado.
Desmanche do Fardão
É realizada a desintegração mecânica do fardão, que pode ocorrer em dois modelos: o primeiro, mais simplificado, consiste no desmanche e no lançamento imediato do algodão na fita transportadora; o segundo agrega a passagem do algodão, após o desmanche inicial, em um batedor inclinado equipado com grelhas (as quais provocam a queda das impurezas menores existentes no produto, como terra e folhas esmagadas), caracterizando um início de limpeza do produto, ainda com o caroço, seguindo então para a fita transportadora.
Pré-limpeza do Algodão
Em geral, o algodão sai da fita de transporte em direção a duas linhas de limpeza. Primeiramente ele passa pelo equipamento mecânico denominado HLST (iniciais em inglês para casca, galhos, folhas e impurezas), o qual promove a retirada de até 70% das impurezas existentes. A seguir, coletado com ar quente, o algodão segue para a torre secadora e para o batedor inclinado, sendo então direcionado para a rosca distribuidora que alimenta o equipamento Cotton King, responsável pela eliminação dos 30% restantes de impurezas da matéria-prima. Algumas algodoeiras são equipadas com válvulas by-pass, as quais evitam a utilização dos equipamentos de pré-limpeza no algodão que chega mais limpo ao beneficiamento, minimizando o batimento da fibra e, consequentemente, contribuindo significativamente na preservação da uniformidade da fibra e na qualidade final da pluma.
Descaroçamento e Limpeza da Pluma
As máquinas de descaroçamento do algodão são o núcleo pulsante da usina de beneficiamento, cujo trabalho contínuo é fundamental para aperfeiçoar o desempenho no processo de obtenção da pluma. Esses equipamentos são dotados de ferramentas denominadas “serras” e “costelas”, além dos rolos de escova que, juntos, engatilham o algodão retendo e separando o caroço, de forma a permitir que a pluma resultante seja liberada para limpeza.
A separação correta dos dois produtos é fundamental para evitar a contaminação da pluma pelo óleo existente no caroço do algodão, um grave contaminante para as fiações, prejudicando tanto o produtor na comercialização quanto a usina na perda de credibilidade do serviço de beneficiamento.
É finalizada a limpeza da pluma por meio da sua separação do ar e entrada no limpador de pluma, onde é penteada e desagregada da fibrilha, um resíduo comum do beneficiamento que pode chegar até a 1,3% do total do algodão em caroço processado.
O caroço do algodão é destinado à armazenagem em salão exclusivo, aguardando sua comercialização e posterior embarque e transporte rodoviário.
Enfardamento e Prensagem
Separada da fibrilha, a pluma é transportada pneumaticamente para uma prensa onde são formados pequenos fardos de algodão, de aproximadamente 200 kg. Os fardos são pesados, recebem etiqueta de identificação com código de barras e têm retiradas de suas laterais duas amostras para a classificação do algodão por laboratório especializado - em Minas Gerais o laboratório responsável é a Central de Classificação de Fibra de Algodão (Minas Cotton), filial da Amipa na cidade de Uberlândia.
Dispostos em salão apropriado ainda dentro da usina, os fardos aguardam a chegada do relatório eletrônico com as análises da fibra e o número do Certificado de Origem e Qualidade do algodão, para que seja liberada a ordem de seu embarque imediato ou empilhamento em armazém ou pátio externo da algodoeira.
As pilhas, organizadas por produtor ou por classificação da pluma, possuem fardos 100% rastreáveis, com histórico completo no qual são lançados em sistema informatizado a entrada do fardão, a pesagem, identificação, classificação, certificação de origem e qualidade, armazenagem.
Certificado de origem e qualidade do algodão
A partir da emissão do relatório de classificação do algodão é liberado o certificado de origem e qualidade do algodão beneficiado, estabelecido pelas normas do Programa Mineiro de Incentivo à Cultura do Algodão (Proalminas).
Caso único de certificação de pluma quanto à procedência e atestado de qualidade para sua comercialização, a medida foi implementada, em 2011, pela Secretaria de Estado da Agricultura, Pecuária e Abastecimento de Minas Gerais (Seapa) por meio do Instituto Mineiro de Agropecuária (Ima) e apoio da Amipa, Minas Cotton, algodoeiras e indústrias têxteis mineiras.
Sistema ABRAPA de Identificação
O SAI, desenvolvido e implantado pela Associação Brasileira dos Produtores de Algodão (Abrapa), em 2004, permite a identificação e procedência dos fardos de algodão, agregando competitividade na comercialização ao identificar o cotonicultor, as características do produto e sua classificação, o que também contribui no atendimento às exigências de qualidade dos principais compradores de qualquer parte do país e do mundo.
O sistema auxilia o trabalho de classificação por HVI (High Volume Instrument), facilitando a identificação das amostras enviadas aos laboratórios para medição dos parâmetros de comprimento, micronaire, uniformidade e resistência.
Baseado no sistema implantado pelo United States Department of Agriculture (USDA) – Departamento de Agricultura dos Estados Unidos -, considerado padrão internacional e aceito por todos os grandes países produtores e consumidores, o SAI evoluiu por meio de parceria com a GS1 Brasil – Associação Brasileira de Automação e, em 2011, passou a utilizar um código de série de unidade logística, padrão SSCC (Serial Shipping Container Code), atualmente um dos mais importantes identificadores de aplicação destinados à rastreabilidade de produtos.
Simples, prático e seguro para rastreabilidade dos fardos de algodão, o novo processo permite que todos os produtores e algodoeiras implantem o sistema sem demandar grandes investimentos.
Vantagens para a Algodoeira
- Oferta de um sistema único e confiável de identificação dos fardos
- Facilidade para vender o algodão ao mercado externo
- Agilidade na obtenção dos resultados da classificação pelos laboratórios
- Participação no processo que será adotado, em curto prazo, por 100% dos beneficiadores, por exigência do próprio mercado e dos clientes, o que poderá afetar economicamente as usinas não cadastradas
Passos para Cadastro no SAI
O cadastro da algodoeira é realizado diretamente pela Abrapa e todas as orientações encontram-se detalhadas no endereço www.abrapa.com.br/sai.
O processo de cadastramento é constituído das seguintes etapas:
- Filiação à GS1 Brasil
- De posse do prefixo liberado pela GS1, poderá ser solicitado o cadastro junto à Abrapa, por carta ou e-mail, juntamente com o envio dos seguintes documentos:
- Solicitação de filiação para Pessoa Física ou Pessoa Jurídica
- Declaração da Associação Estadual confirmando a existência da algodoeira
- Cópia da Inscrição Estadual e CNPJ da usina/algodoeira
- Cópia do RG e CPF do(s) proprietário(s)
- Cópia do contrato social
- Cópia da carta de liberação do prefixo GS1
- Ficha de cadastro da usina/algodoeira
- Ficha de cadastro de cada prensa
- Comprovante de endereço para correspondência
- Nome do responsável por solicitar as etiquetas e manter o sistema atualizado, juntamente com dados para contato (telefones e e-mail)
- Outros documentos que se fizerem necessários, de acordo com cada caso.
- Habilitação do usuário e fornecimento da senha para acesso ao SAI, pela Abrapa
- Impressão e assinatura, pelo responsável legal ou procurador da usina, com firma reconhecida, do Termo de Compromisso gerado no primeiro acesso ao SAI e seu envio à Abrapa
- Após o recebimento do Termo de Compromisso, concretização do cadastro para realização de pedidos de etiquetas
Informações adicionais podem ser obtidas por meio do telefone (61) 3028-9700 ou pelo e-mail abrapa@abrapa.com.br.
Fonte: AMIPA/ABRAPACiclo detalhado do Beneficiamento do Algodão
O beneficiamento do algodão ocorre em várias etapas. Após colhido e compactado em módulos é direcionado para os seguintes equipamentos que compõe o “Ciclo do Beneficiamento”.
1.Descompactador de Fardos
Neste equipamento o algodão que está em módulos de 12 metros de comprimento, por 3 metros de largura e por 3 metros de altura é descompactado por cilindros recobertos com pinos de aço que ao extrair o algodão, impulsionam o mesmo contra grelhas que fazem uma limpeza inicial. Neste estágio parte das impurezas como: galhos, folhas, pedriscos e terra são removidos e expelidos para fora do equipamento enquanto o algodão segue para o próximo estágio.
2.Ventilador de sucção
Este equipamento tem a finalidade de sugar o algodão através da tubulação até a Válvula VRS 1.
3.Válvula VRS 1
A Válvula em questão distribui o algodão e também retira impurezas mais pesadas que estão soltas do algodão.
4.Válvula Droop 1
Esta válvula faz o corte do ar que suga o algodão até a válvula VRS 1 que leva por gravidade para Coluna Secadora.
5.Coluna Secadora
A Coluna Secadora como o próprio nome diz tem a finalidade de secar o algodão. É nesta etapa que se faz a correção da umidade do algodão para que haja uma maior eficiência nas próximas etapas. O fato de o algodão passar pelas 24 gavetas faz com que o algodão fique solto e siga de uma forma mais uniforme e distribuída. O transporte do algodão dentro deste equipamento é feito com o auxílio do Ventilador Secador.
6.Ventilador Secador
Este ventilador impulsiona o algodão para dentro da Coluna Secadora forçando a passar pelas 24 gavetas e o conduz até ao Batedor inclinado 1.
7.Batedor Inclinado 1
Nesta etapa o Algodão é batido literalmente contra as grelhas e separado das fibras, galhos, folhas e outras partículas que prejudicariam os processos posteriores. Nesta etapa as impurezas são segregadas do processo.
8.Batedor Inclinado 2
Tem a mesma finalidade do batedor Inclinado 1. Torna-se necessário em função do grande volume de algodão e proporcionando uma melhor limpeza. Nesta etapa as impurezas também são segregadas do processo.
9.HLST
Este equipamento é de fundamental importância no processo, pois é o responsável pela remoção das cascas e folhas que estão aderidas à pluma do algodão. Nesta etapa as impurezas também são segregadas do processo.
10.Válvula Droop 2
Esta válvula faz o corte do ar que Recalcou o algodão através dos Batedores Inclinados e o transporta em vácuo para uma câmara onde será sugado até a Válvula VRS 2.
11.Ventilador de Sucção do fundo da Válvula
Este ventilador suga o algodão até a Válvula VRS 2.
12.Válvula VRS 2
Tem a mesma função da Válvula VRS 1, ou seja, distribui o algodão e também retira impurezas mais pesadas que estão soltas do algodão.
13.Válvula Droop 3
Esta válvula faz o corte do ar que sugou o algodão até a Válvula VRS 2 e o transporta em vácuo para uma câmara onde cairá por gravidade na Calha da Rosca Distribuidora.
14.Rosca Distribuidora
A distribuição do algodão nos Super Mitchells é feita pela Rosca Distribuidora e o algodão excedente é levado até a Torre de Sobra.
15.Torre de Sobra
A Torre de sobra como o próprio nome já diz, serve para redistribuir o algodão excedente novamente na calha da Rosca sem que o algodão passe novamente pelos processos anteriores, preservando inalteradas as propriedades do algodão. Outra vantagem apresentada neste equipamento é o fato de se conseguir um maior controle na distribuição do algodão, consecutivamente, melhor controle de alimentação das máquinas. Este controle é feito graças a Válvula de alimentação e uma Válvula Droop.
16.Válvula de Alimentação
Está válvula tem a função de dosar a Redistribuição do Algodão.
17.Válvula Droop 4
Esta válvula tem a função de isolar a Válvula de Alimentação do ar que transporta o algodão até a Válvula VRS 3.
18.Ventilador de Sucção do Fundo da Válvula.
Este ventilador suga o algodão que sai da torre de sobra até a válvula VRS 3 que posteriormente ira redistribuir o algodão na Calha da Rosca.
19.Válvula VRS 3
Tem a mesma função das válvulas VRS 1 e 2 .
20.Válvula Droop 5
Esta válvula faz o corte do ar que recalcou o algodão até a Válvula VRS 3 e o transporta em vácuo para uma câmara onde cairá por gravidade na Calha da Rosca Distribuidora.
21.Super Mitchell
Neste equipamento a casca do algodão é Retirada, bem como as impurezas que não foram totalmente extraídas da pluma. O sistema de rolos com serrilhas proporciona uma limpeza mais apurada, deixando para o Descaroçador apenas a pluma e o caroço. Nesta etapa as impurezas são segregadas do processo e transportada através de uma calha, que é comum para todos os Mitchells e em seguida é recalcado por ar para um local apropriado pelo Ventilador da Casca. Posteriormente esta Casca será transformado em adubo orgânico.
22.Ventilador da Casca
Responsável pelo transporte da casca até o local destinado para armazenamento.
23.Descaroçador 90 Serras
Este equipamento é o responsável pelo descaroçamento do algodão. As serras removem a pluma do caroço e quando o caroço estiver desprovido de pluma, o mesmo cai por gravidade na Rosca do Caroço que é transportado até o final da calha para posteriormente ser transportado por ar até o salão de caroço pelo ventilador do Caroço. Já a Pluma é extraída das serras por jato de ar que é obtido através do ventilador de Recalque.
24.Ventilador de Recalque
Responsável pela geração do jato de ar que extrai a pluma da serra e também pelo recalque do condensador do Limpador de Pluma.
25.Ventilador de Caroço
Responsável pelo transporte da casca até o local destinado para armazenamento.
26.Exaustores de Sucção 1 e 2
Estes exaustores proporcionam a sucção da pluma até o Condensador do Limpador de Pluma 1 e 2 juntamente ao Ventilador de Recalque (24).
27.Limpadores de Pluma 1 e 2 com Condensadores
Condensador modela a pluma numa única manta uniforme para que posteriormente seja processada no limpador de plumas de maneira equalizada. O Limpador de Pluma faz a limpeza final da pluma retirando as fibras mortas (fibrilha) e algumas mínimas sujeiras que escaparam aos processos anteriores. A fibrilha é transportada para o Batedor de Fibrilha com o auxílio do ventilador de Fibrilha.
28.Ventilador de Fibrilha
Responsável pelo transporte da Fibrilha até o Batedor de Fibrilha.
29.Batedor de Fibrilha
Responsável pela limpeza da Fibrilha.
30.Exaustor de Sucção 2
Este exaustor suga o algodão vindo do Limpador de Pluma e o transporta até o Condensador.
31.Condensador
Este equipamento condensa o algodão em uma única manta uniforme para ser prensado.
32.Empurrador Pneumático
Responsável pelo transporte sincronizado do algodão até o Calcador mantendo o algodão em mantas para posterior prensagem.
33.Calcador Mecânico
Este equipamento faz a pré-compactação do Algodão para posteriormente ser prensado em definitivo pelo Pistão do Cilindro Ø 12 polegadas.
34.Prensa Hidráulica
Este equipamento faz a compactação do algodão em fardos de 200 Kg. Esta prensagem é obtida pelo Cilindro Hidráulico de Ø 12 polegadas e acionado pela Unidade Hidráulica.
35.Cilindro Hidráulico Ø 12 polegadas
É o responsável pela prensagem do fardo de pluma.
36.Unidade Hidráulica
É o equipamento que aciona o pistão do Cilindro Hidráulico Ø 12 polegadas. Tem capacidade de prensagem de 01 minuto por ciclo.
37.Ensacador de Fardos
Este equipamento reduz o set up entre um fardo e outro, proporcionando maior agilidade aos operadores de prensa e ampliando a capacidade de prensagem.
TRATAMENTO DE IMPUREZAS
As impurezas retiradas durante o benefício do algodão são tratadas da seguinte forma :
No Descompactador de Fardos:
São recolhidas manualmente e descartadas em lugares apropriados.
Nas Válvulas VRS
São transportadas por ar até os Ciclones de Tratamento de Impurezas (casa de pó).
Nos Batedores Inclinados
As impurezas retiradas neste processo são transportadas por ar até a tubulação de casca vinda dos Mitchells e de lá seguem para depósito apropriado e posteriormente são transformadas em adubo orgânico.
No HLST
Assim como nos Batedores Inclinados, as impurezas retiradas neste equipamento são transportadas por ar até a tubulação de casca vinda dos Mitchells e de lá seguem para depósito apropriado e posteriormente são transformadas em adubo orgânico.
Nos Descaroçadores
A Fibra morta ou “Piolho” pode ser descartada juntamente ao Caroço que é transportado até o salão de Caroço ou segregada e depois embalada separadamente. Entre as utilizações possíveis para o caroço do algodão, estão o uso em ração animal, fabricação de óleo, entre outros.
Nos Limpadores de Pluma
As impurezas bem como a fibrilha são transportadas por ar até o Batedor de Fibrilha que faz a limpeza da Fibrilha que depois é embalada.
Exaustores
As impurezas sugadas pelos Exaustores são enviadas até os Ciclones de Tratamento de Impureza, que são limpos a cada 06 à 10 dias.
As demais operações não causam ou deixam resíduos que precisem ser tratados separadamente e são limpas manualmente ao final de cada turno.
Fonte Candeloro
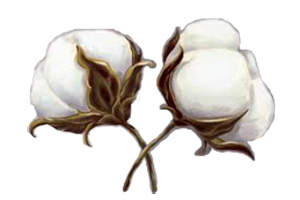
Tipo do Algodão em Pluma
Descrição | Tipo |
---|---|
Cor boa média ( good middling ) | 11 |
Cor estritamente média ( strict middling ) | 21 |
Cor média ( middling ) | 31 |
Cor estritamente abaixo da média ( stric low middling ) | 41 |
Cor abaixo da média ( low middling ) | 51 |
Cor estritamente boa comum ( strict good ordinary ) | 61 |
Cor boa comum ( good ordinary ) | 71 |
Abaixo de padrão ( below grade ) | 81 |
Utilizações Industriais da Fibra do Algodão
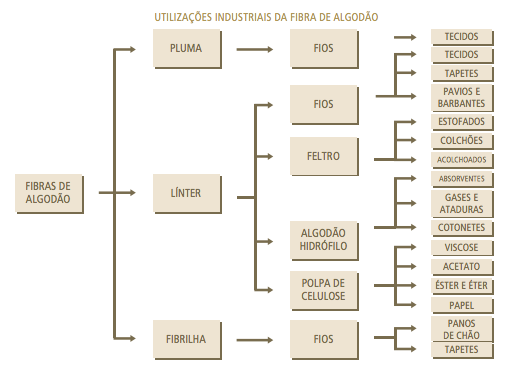
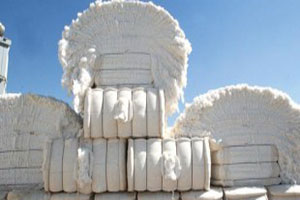
Embalagem em Fardo
Depois da pré-limpeza, retirada do Caroço e de todos os processos do beneficiamento, o Algodão em Pluma é prensado em fardos é comercializado neste tipo de embalagem.
Resíduos e Sub-produtos do Algodão
Usina de Beneficiamento
|
Fiação
|
Na Indústria de Óleos
|